High-Performance
Aluminum Ingot Scalping Machines





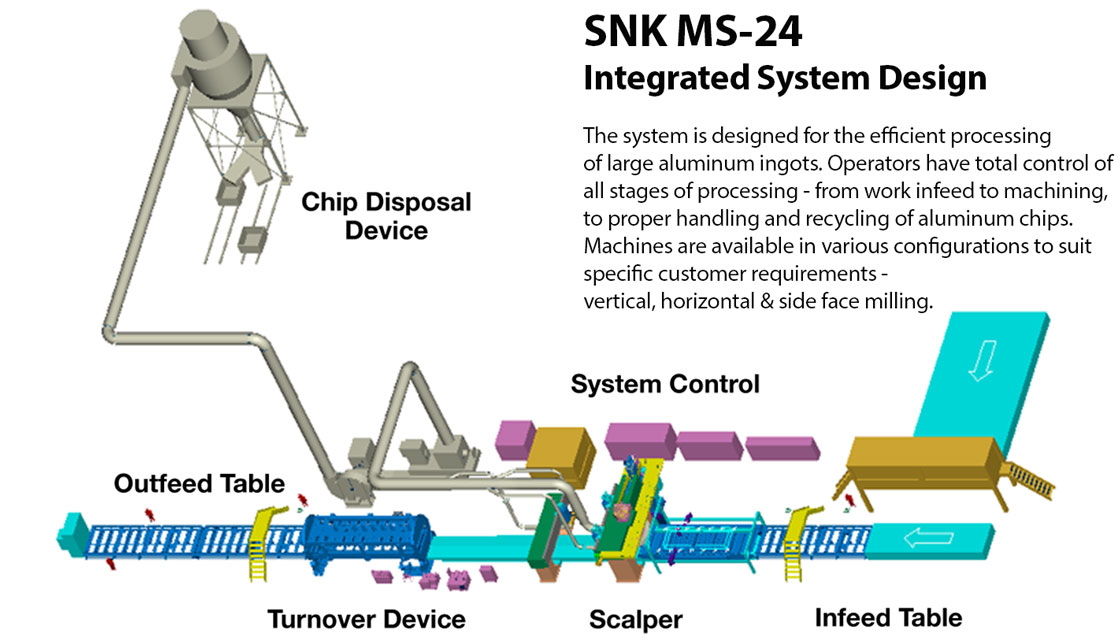
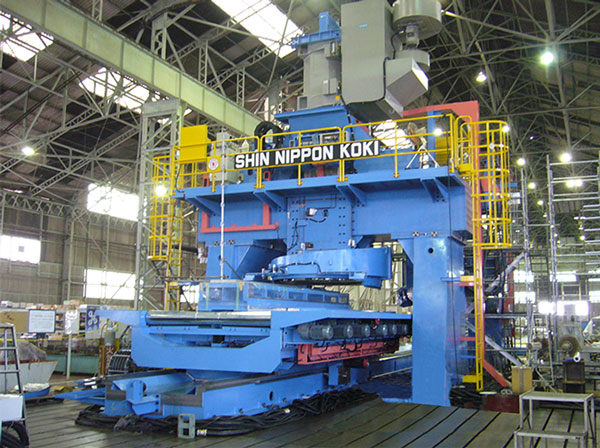
The SNK MS-24
Aluminum Ingot Scalper System delivers these key benefits:
- Optimum production productivity
- Production cost savings
- Superior machining quality (mirror finish)
- Environmental protection
- Energy savings
SNK MS-24
Expanded Cutting Capability
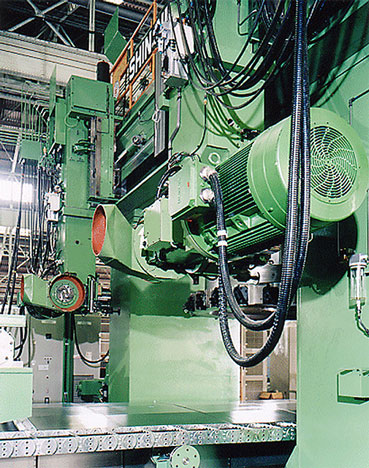
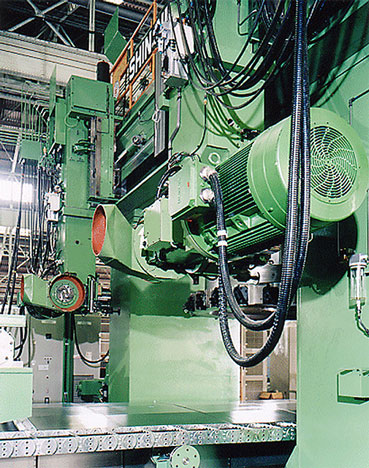
SNK MS-24
Expanded Cutting Capability
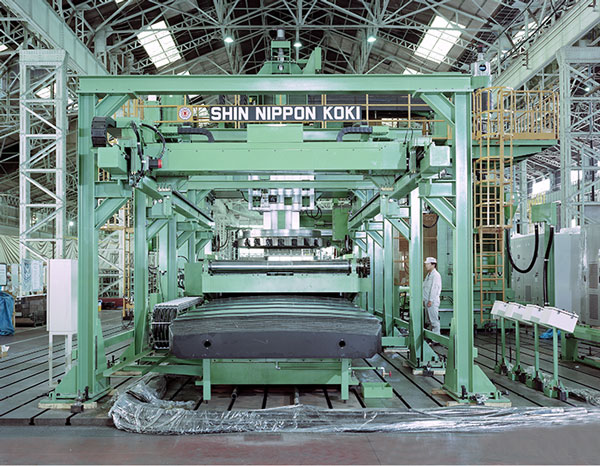
SNK
Streamlined Work Handling
The infeed table provides for easy loading of the workpieces and feeds ingots into the machining work envelope. The outlet table facilitates easy work unloading after machining.
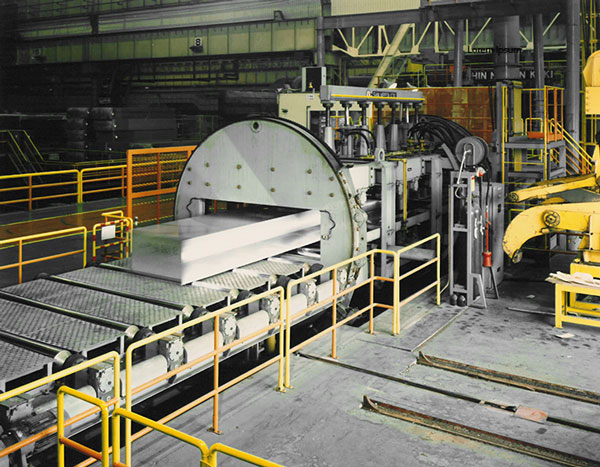
Optional Turn-Over Device
The optional workpiece turn-over device prepares the ingot for bottom face processing.
SNK
Efficient Spindle Design & Cutter System
Cartridge type cutting inserts streamline insert exchange
and simplify cutting depth adjustment.
- Vertical spindle: 2400mm (94.5”) dia. / 20 blades
- Horizontal spindles: Two 400mm (15.75) dia. / 6 blades each head
- Spindle runs at 100rpm during standby – saves energy
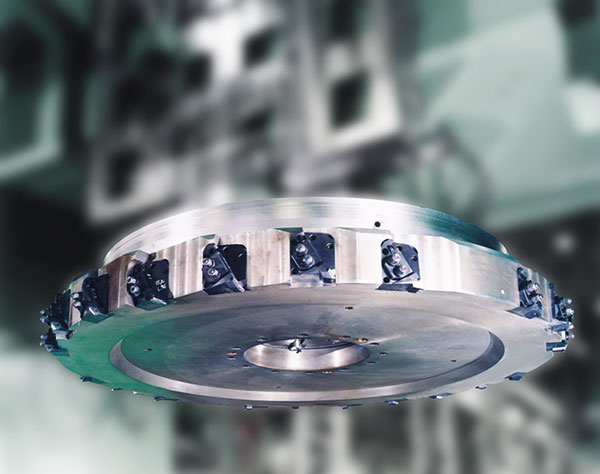
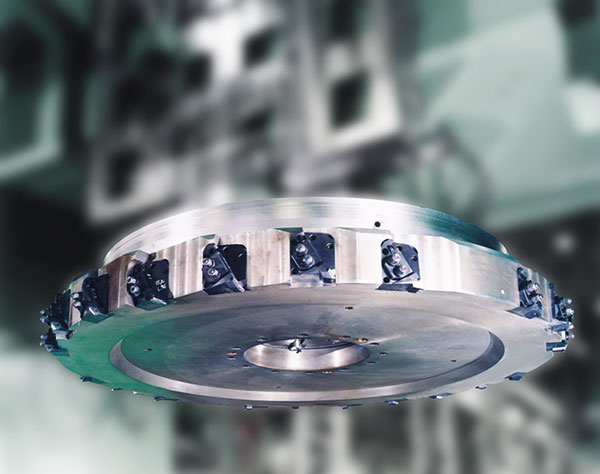
SNK
Efficient Spindle Design & Cutter System
Cartridge type cutting inserts streamline insert exchange and simplify cutting depth adjustment.
- Vertical spindle: 2400mm (94.5”) dia. / 20 blades
- Horizontal spindles: Two 400mm (15.75) dia. / 6 blades each head
- Spindle runs at 100rpm during standby – saves energy
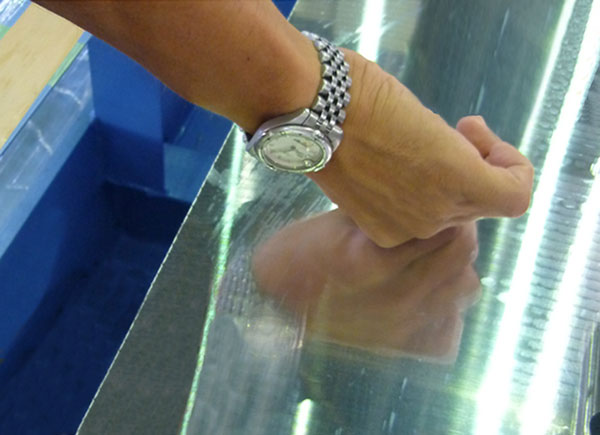
SNK
Superior Machined Finish Quality
The high-horsepower, high-speed low torque spindle features cutting speeds of 3,000 to 4,000 m/min (118,110 to 157,480 ipm) surface speed.Cutting feedrate is 500 to 7,000 mm/min (19 to 275 ipm). Mirror finish surfaces are attainable under ideal cutting conditions.
SNK
High-Performance
Chip Management System
99% of chips are collected by the mantel located above the milling head. Remaining chips are pushed into a chute by a table stroke/scraper system. Switchable chip chutes assure varied materials are kept separate. In addition, a high efficiency dust collector minimizes the release of aluminum into the air.
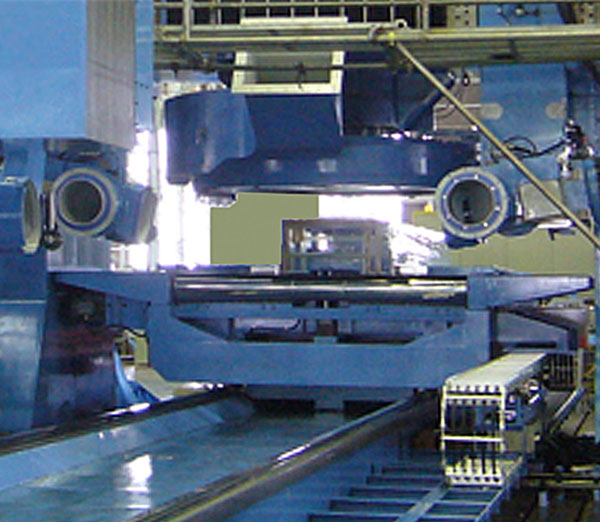
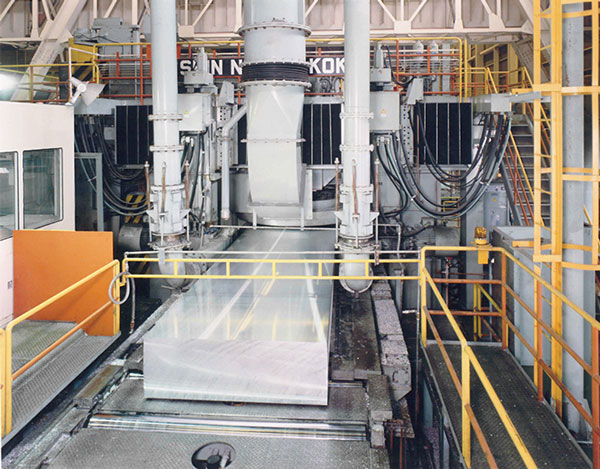
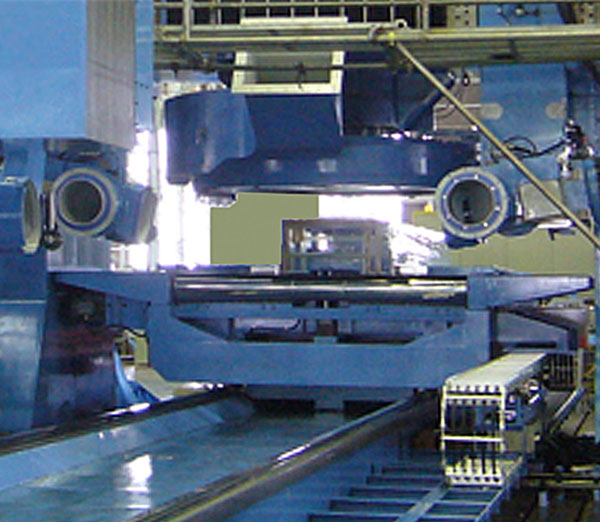
SNK
High-Performance
Chip Management System
99% of chips are collected by the mantel located above the milling head. Remaining chips are pushed into a chute by a table stroke/scraper system. Switchable chip chutes assure varied materials are kept separate. In addition, a high efficiency dust collector minimizes the release of aluminum into the air.
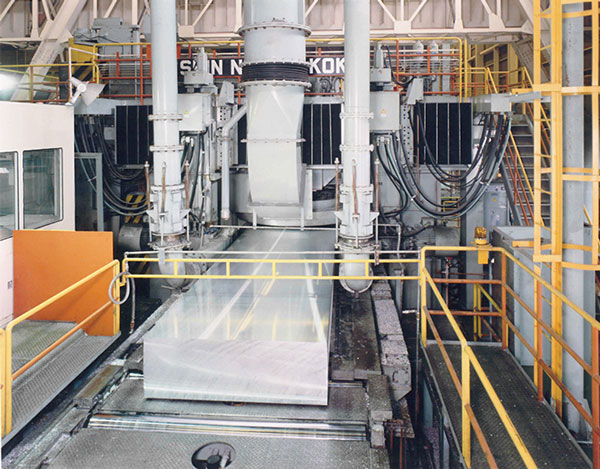